November 22, 2023
Making Midstream future-ready: Transform Midstream Operations with a Digital Twin
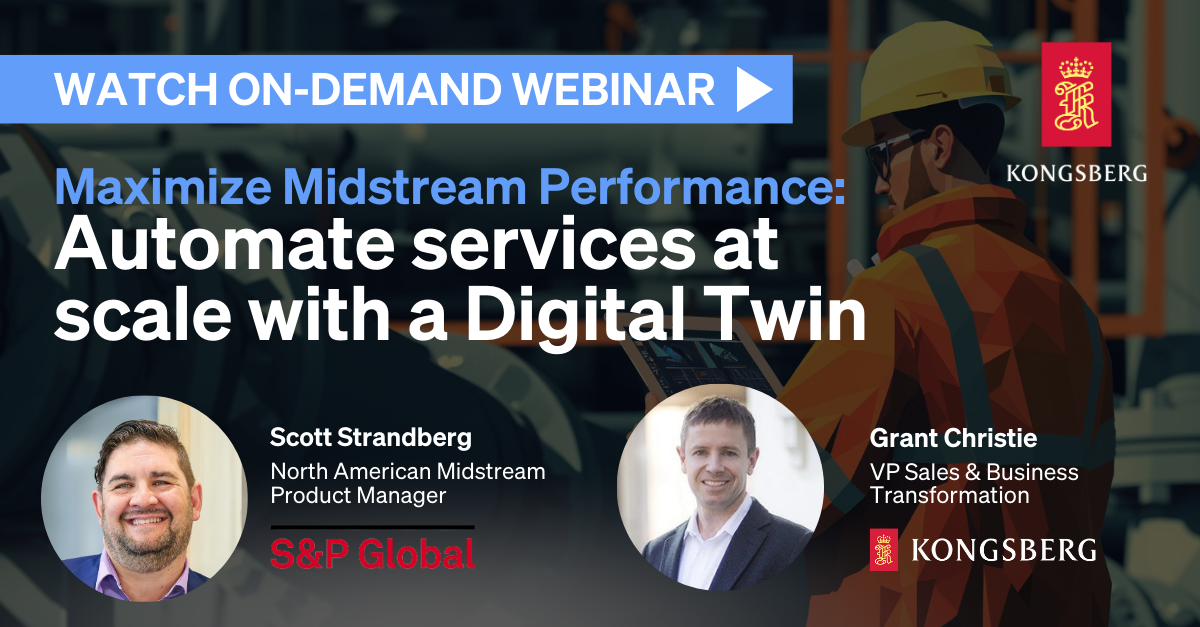
Aging pipeline infrastructure comes at a high price , with pipeline incidents between 2001 and 2020 causing as much as USD 10.7 billion worth of damages during the time period.
What exactly is a digital twin?
Before diving into what this technology could mean for midstream, here’s a quick rundown of how we see digital twins for heavy asset industries.
A digital twin is a cloud-based solution that uses data to create a realistic and highly accurate digital version of an asset, facility, or vessel, including its layout and components right down to equipment pieces and nuts and bolts. Users can access a single environment on any web-enabled device to virtually explore an overview of all company assets, one specific asset, search for information, run entire workflows, and collaborate with other users remotely.
Capabilities of a digital twin for industrial assets
- Single integrated environment for one or multiple assets – no need for multi-system or paper-based planning
- Customisable dashboards showing data most relevant to the user
- Features, capabilities, and interactions that mirror the everyday technology experiences we have when using mobile phones and laptops
- Orchestration of workflows to drive insights, plan activities, monitor performance and ensure safe operations
- Enriched Data Lake that ingests data sources and makes them understandable to a wide scope of users
- Integrates data sources and formats including PDMS, CAD; point clouds, photogrammetry, imaging, scan, GIS, etc.
- Visual overview of industrial data including maintenance records, historical and real-time data
- Powerful real-time, simulation, and AI/ML models
- Enables workflow execution including Proactive Technical Monitoring, Performance Monitoring, Virtual Measurements, Isolation Planning, Supply Chain Optimisation, and Emissions Management
- Cloud-based Software as a Service (SaaS) solution
Getting value from big data
When looking at the almost infinite amount of data available to midstream companies, it becomes clear that technology can help reduce complexity to truly unlock the value of this data – especially considering the increasingly dispersed data landscape in midstream. As companies expand through acquisitions, each brings its own set of systems, technologies, and data management practices to the table. Over time, this leads to a complex and fragmented data environment, leaving important information scattered across various platforms and databases.
A lack of standardisation and interoperability further complicates the data management challenge. A digital twin provides a place for midstream operators to integrate data sources and foster a holistic understanding of operations through data contextualization and visualisation supported by advanced analytics.
.png)
The many records, documents, drawings, images, reports, and schedules across a facility – right down to the data connected to a single piece of equipment – can be brought together in one digital environment and displayed in a way that makes sense to different levels of users.
Digital twin benefits to increase the value of data for midstream operators:
Single source of truth
Connect existing data sources in one place to get insights into daily operations, trends, and demand patterns. Low data maturity or missing data issues are overcome by synthetic data and advanced algorithms that can monitor operations and predict optimal parameters.
Remote access
Log in to the digital twin from anywhere in the world to access site data remotely and collaborate with users in different geographical locations.
Situational awareness
In a digital twin, data is contextualized, made searchable and visualized (3D, 2D, Photogrammetry Laser Scans, GIS etc.). This gives users true situational awareness, enabling them to zoom, navigate the site and take measurements.
Pipelines, performance, and the power of prediction
Many of North America’s largest pipeline companies operate pipeline systems that were installed more than fifty years ago. For aging infrastructure, digital twins offer rewarding opportunities for better performance, more focused maintenance, and improved asset integrity.
Workflows like Performance Monitoring and Proactive Technical Monitoring in a digital twin make it possible to monitor equipment and assets at a midstream facility over time to evaluate baseline trends and deviations. This helps operations teams and engineers with the early identification of technical issues in processing plants and pipelines, ensuring timely intervention and avoidance of critical equipment failure.
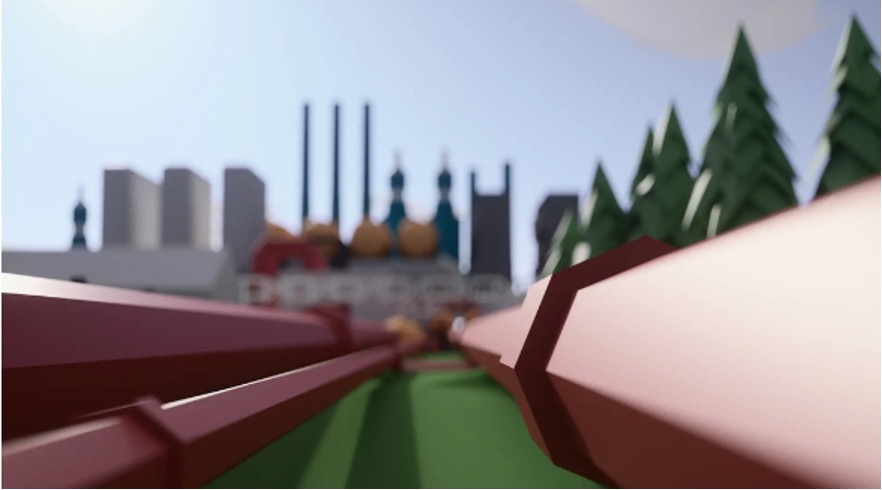
On-site activities can be expedited or deferred based on real-time data-driven assessments in the twin, and data from steady-state and dynamic simulators can predict operational parameters for equipment to improve energy usage and drive improvements in terms of efficiency and emissions reduction.
Digital twin benefits to midstream operators:
Increase throughput volumes
By simulating various scenarios and leveraging real-time data, the twin can identify potential capacity improvements and enable more informed decision-making. Implement preventive measures in high-risk areas, schedule maintenance strategically, and ensure a continuous flow of resources through the midstream infrastructure.
Maintenance cost reduction
Always-on monitoring of system performance across midstream processes enables operators to go from reactive to predictive maintenance. That means operators can get insights into the performance of equipment like process heaters, furnaces, and boilers and use these to drive optimisations, address technical issues early on and reduce emissions.
Proactive technical monitoring
Monitor pipelines, pumps, and vessels and visualize the location of maintenance priorities. Just-in-time maintenance helps prolong the lifetime of equipment and avoids production disruptions due to technical issues.
Simulations
Use powerful simulation capabilities to run what-if scenarios under various operating conditions. Practice and prepare for any scenario, without costly investments or posing a risk to people and the environment.
Alert! Learn about dynamic simulators for midstream use cases in our upcoming blog posts. Follow our LinkedIn page for the latest updates
ESG, emissions, and engaging in the energy transition
Increasing pressure and expectations to operate more sustainably – not only in terms of regulatory requirements but also the expectation of delivering renewable fuels at scale for the future – could have serious ramifications when it comes to capital investments, supply chain reliability, and energy costs to end customers. Emerging demands from governing authorities require technology adoption and new investments, while negative perceptions around the oil and gas industry’s seeming inability to operate greener deprive midstream operators of much-needed investment possibilities.
Digital twins with workflow support for emissions management, supply chain optimization, and streamlined resource allocation can help midstream companies scale alongside growing ambitions to play a part in the energy transition. They also open new opportunities for companies to collaborate and innovate at a higher level to further the industry’s common goal of a safer, smarter, and more sustainable tomorrow.
.jpeg)
Digital twin benefits to midstream operators:
Emissions reduction
Use emissions management features to understand and benchmark emissions to drive improvements and gather information for reporting purposes.
Workflow support
Optimise materials management, logistical operations and equipment tracking. Find new opportunities for data-driven simplification and the automation of manual and repetitive work tasks.
Build a foundation for the future
Equip users with digital technology that helps enable the energy transition and allows for the integration of new technology innovations like IoT devices, drones and wearable equipment.
Keep things flowing
Would you like to learn more about how our technology can drive value for your company or see a demo?
Fill in the form below and we’ll put you in touch with one of our midstream experts so that you can deploy, scale, and benefit from our world-class solutions that are already helping major energy players succeed.
Author
Yorinde Lokin-Knegtering
Growth Manager Americas
Related news
2 July 2025
Unifying the Oil & Gas Value Chain: How Data + AI Power Performance
19 June 2025
Data Driven Oil & Gas 2025: Insights and expectations from Kongsberg Digital
21 May 2025
Reshaping the future of work in energy
28 November 2024
Co-Innovation, Digital Transformation, and AI in Oil and Gas: Insights from WECA